Ultrasonic Inspection (UT)
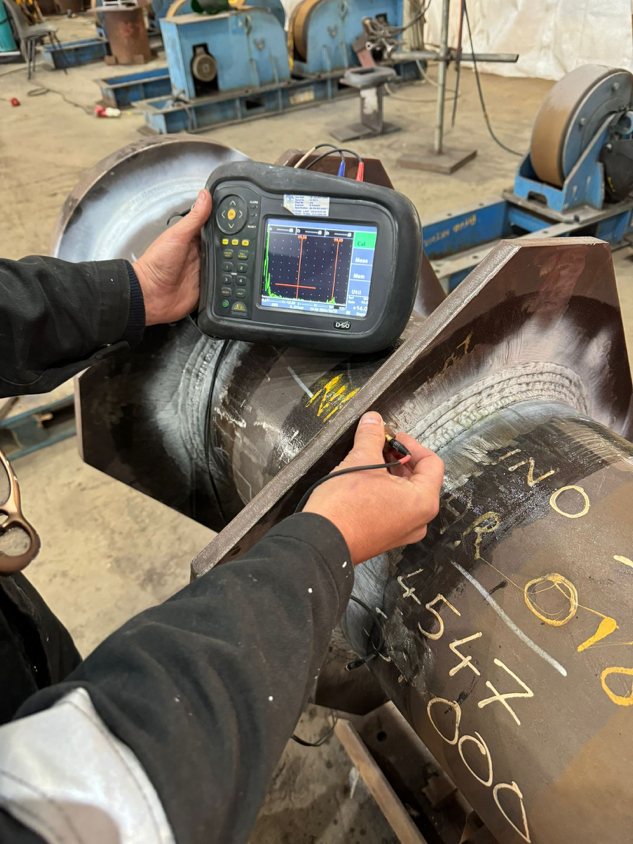
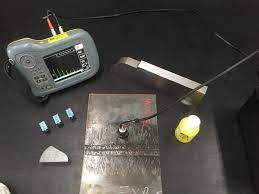
Ultrasonic Inspection (UT)
Usually, pulsed beams of ultrasound are used and in the simplest instruments a single probe, hand-held, is placed on the specimen surface. An oscilloscope display with a time-base shows the time that it takes for an ultrasonic pulse to travel to a reflector (a flaw, the back surface, or other free surface) in terms of distance across the oscilloscope screen – the so-called A-scan display. The height of the reflected pulse is related to the flaw size as seen from the transmitter probe. The relationships of flaw size, flaw distance and flaw reflectivity are complex and considerable skill is required to interpret the display.
Complex multiprobe systems are also used with mechanical probe movement and digitisation of the signals, followed by computer storage; methods of computer interpretation are developing rapidly.
There are several forms of mechanical vibration, depending on the direction of particle movement in the wave motion, and so there are several forms of ultrasonic waves, the most widely used in NDT being compressional and transverse (shear) waves.
Complex multiprobe systems are also used with mechanical probe movement and digitisation of the signals, followed by computer storage; methods of computer interpretation are developing rapidly.
There are several forms of mechanical vibration, depending on the direction of particle movement in the wave motion, and so there are several forms of ultrasonic waves, the most widely used in NDT being compressional and transverse (shear) waves.
By suitable design of probe, ultrasonic beams can be introduced into solid material at almost any angle.
Generally, a single probe acts as both transmitter and receiver, so that inspection can be done from one side only of the specimen. Large-grain materials such as austenitic steel welding, copper castings etc produce severe attenuation and scattering and are at present difficult to inspect with ultrasound, but large thicknesses of fine-grain material such as forged steel can be tested without difficulty.
Ultrasonic attenuation and ultrasonic velocity measurements are used to study various material properties.
The use of ultrasonics for sizing flaws
Once flaws have been detected it is often desirable to determine their size. For flaws smaller than the ultrasonic beam width, a pseudo-sizing can be obtained by comparing the flaw signal amplitude with that of a reference reflector (flat-bottomed or side-drilled hole) at the same range. When the flaw size is greater than the ultrasonic beam width, conventional probe movement sizing techniques can often be used to provide an estimate of flaw size. The maximum amplitude technique uses a measure of the probe movement between the maximised signals from flaw extremities to size flaws. The 6 dB and 20 dB drop techniques use the reduction in the signal amplitude from the flaw as the probe passes over the edge of the flaw as an indicator of flaw dimensions. However, the interaction between the ultrasonic beam and flaw, depending as it does on flaw nature and orientation, limits the effectiveness of these techniques, when dealing with complex and mis-orientated flaws.
Techniques which make use of the diffracted signal from the flaw extremities to locate and size flaws are most effective in sizing planar flaws.
Generally, a single probe acts as both transmitter and receiver, so that inspection can be done from one side only of the specimen. Large-grain materials such as austenitic steel welding, copper castings etc produce severe attenuation and scattering and are at present difficult to inspect with ultrasound, but large thicknesses of fine-grain material such as forged steel can be tested without difficulty.
Ultrasonic attenuation and ultrasonic velocity measurements are used to study various material properties.
The use of ultrasonics for sizing flaws
Once flaws have been detected it is often desirable to determine their size. For flaws smaller than the ultrasonic beam width, a pseudo-sizing can be obtained by comparing the flaw signal amplitude with that of a reference reflector (flat-bottomed or side-drilled hole) at the same range. When the flaw size is greater than the ultrasonic beam width, conventional probe movement sizing techniques can often be used to provide an estimate of flaw size. The maximum amplitude technique uses a measure of the probe movement between the maximised signals from flaw extremities to size flaws. The 6 dB and 20 dB drop techniques use the reduction in the signal amplitude from the flaw as the probe passes over the edge of the flaw as an indicator of flaw dimensions. However, the interaction between the ultrasonic beam and flaw, depending as it does on flaw nature and orientation, limits the effectiveness of these techniques, when dealing with complex and mis-orientated flaws.
Techniques which make use of the diffracted signal from the flaw extremities to locate and size flaws are most effective in sizing planar flaws.