Dye Penetrant Inspection (DPI)
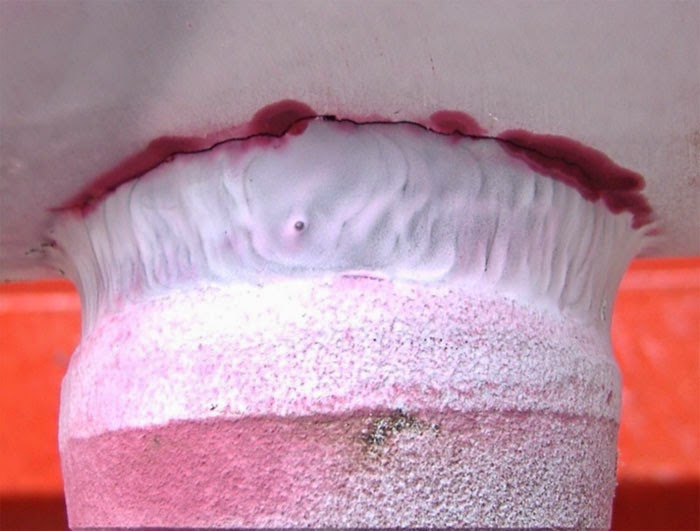
Dye Penetrant Inspection (DPI)
It is usually a six-stage process:
a) surface cleaning (degreasing etc)
b) application of a penetrant liquid (dipping, spray, brush)
c) removal of excess penetrant (solvent, water)
d) application of developer
e) inspection of test surface (visual, television camera)
f) post-inspection cleaning (anti-corrosion solutions).
There are three major groups of penetrant process:
a) water-soluble
b) post-emulsifiable with water rinsing
c) solvent removable, the difference being in the method used to remove the excess penetrant.
In each of these three groups the penetrant solution can contain a dye to make the indication visible under white light, or a fluorescent material which fluoresces under suitable ultraviolet (UV-A) light.
The choice of technique for any specific application is based on:
a) the surface finish of the specimen
b) the compatibility of the materials with the specimen
c) the sensitivity required
d) the size, shape and accessibility of the area to be inspected
e) the ultimate use of the component.
Fluorescent penetrants are usually used when the maximum flaw sensitivity is required.
The principle of liquid penetrant testing is that the liquid penetrant is drawn into the surface-breaking crack by capillary action and excess surface penetrant is then removed; a developer (typically a dry powder) is then applied to the surface, to draw out the penetrant in the crack and produce a surface indication. Cracks as narrow as 150 nanometres can be detected. The indications produced are much broader than the actual flaw and are therefore more easily visible.
Liquid penetrant testing can be applied to any non-porous clean material, metallic or non-metallic, but is unsuitable for dirty or very rough surfaces. Surface cleaning is a vital part of the penetrant testing technique. The method can be manual, semi-automatic or fully automated. Penetrant inspection, continuous-operation production lines in which the specimens are cleaned, dipped, washed, dried, etc on a time cycle are common.
Recently, equipment to fully automate the visual inspection stage of the process, by robotic handling of the specimen on a programmed procedure with television camera viewing and pattern recognition to identify and recognise flaws, has been introduced. Television image enhancement processes can be included.
A special, very high sensitivity penetrant process, using radioactive tracers is sometimes used, but requires very stringent safety procedures.
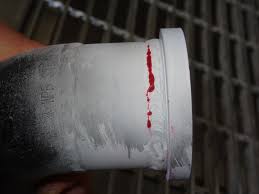
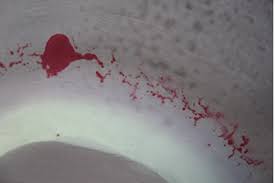
Dye Penetrant Inspection (DPI)
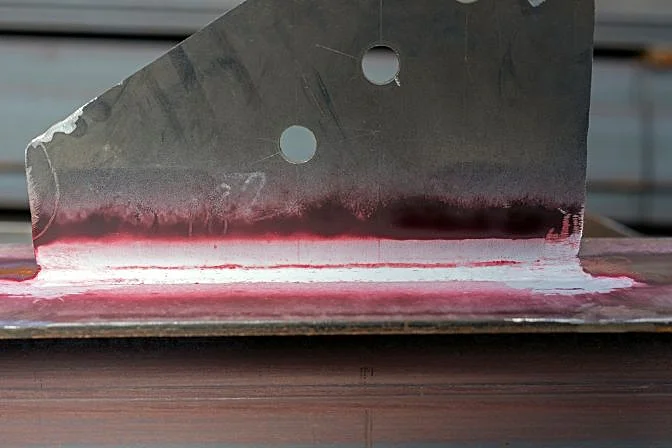